測定精度についてのお問い合わせを頂くことが御座います。
例えば被測定物が停止している状態であれば標準原器を用いて測定し、その絶対精度を確認することも可能ですが、工具は回転しており、振れや工具自体の製造精度も有ります。そこで絶対精度がどの程度なのかをルビーボールΦ6mmの半径Rを180°測定します。
(単位はミクロンですので下3桁はナノメートルになります)
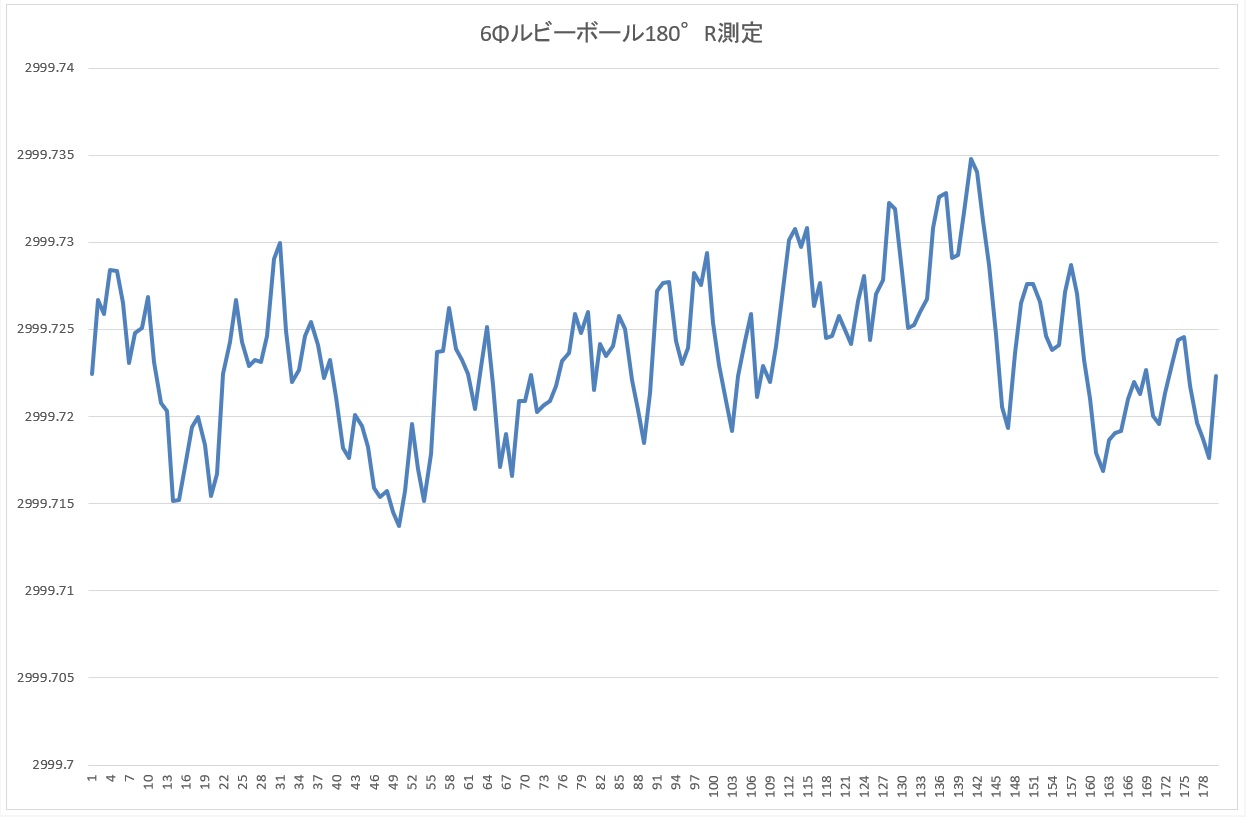
2999.713から2999.735までの間に収束致します。この測定は、主軸に6mmΦルビースタイラスをチャックさせ無回転の状態で測定したものです。外乱光の影響を受けない環境でジェイコアで測定したものですので一般的な加工現場との整合性は有りません。
では実際の加工現場ではどうなのでしょうか。
下記の画像は牧野フライス製作所様製のV33iにてジェイコアで測定を行い補正を自動で掛けさせ加工を行ったものです。
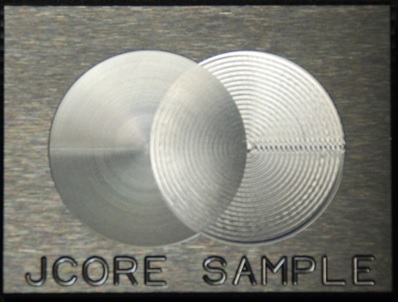
左:0.5Rボールエンドミル・28,000rpm 右:0.5Rラジアスエンドミル・2,700rpm
左右の段差は接触式変位計で0.0と表示されました。最小表示分解能が0.1μmでしたので、それ未満に収束しているものと考えられます。
実際に加工現場で必要な加工精度は、停止しているものを測定する前者ではなく加工回転数域で測定を行う後者になります。勿論加工機械や環境によって仕上がり精度には差異が生じると考えられますが2010年に導入されたV33iで有ることを付け加えておきます。
今回の加工は底面加工でしたが、ルビースタイラスの測定結果から鑑みますと底面だけでなく、斜面や自由曲面における三次元補正も可能だと考えられます。